Noticias
Audi comenzó la fabricación en serie de motores eléctricos
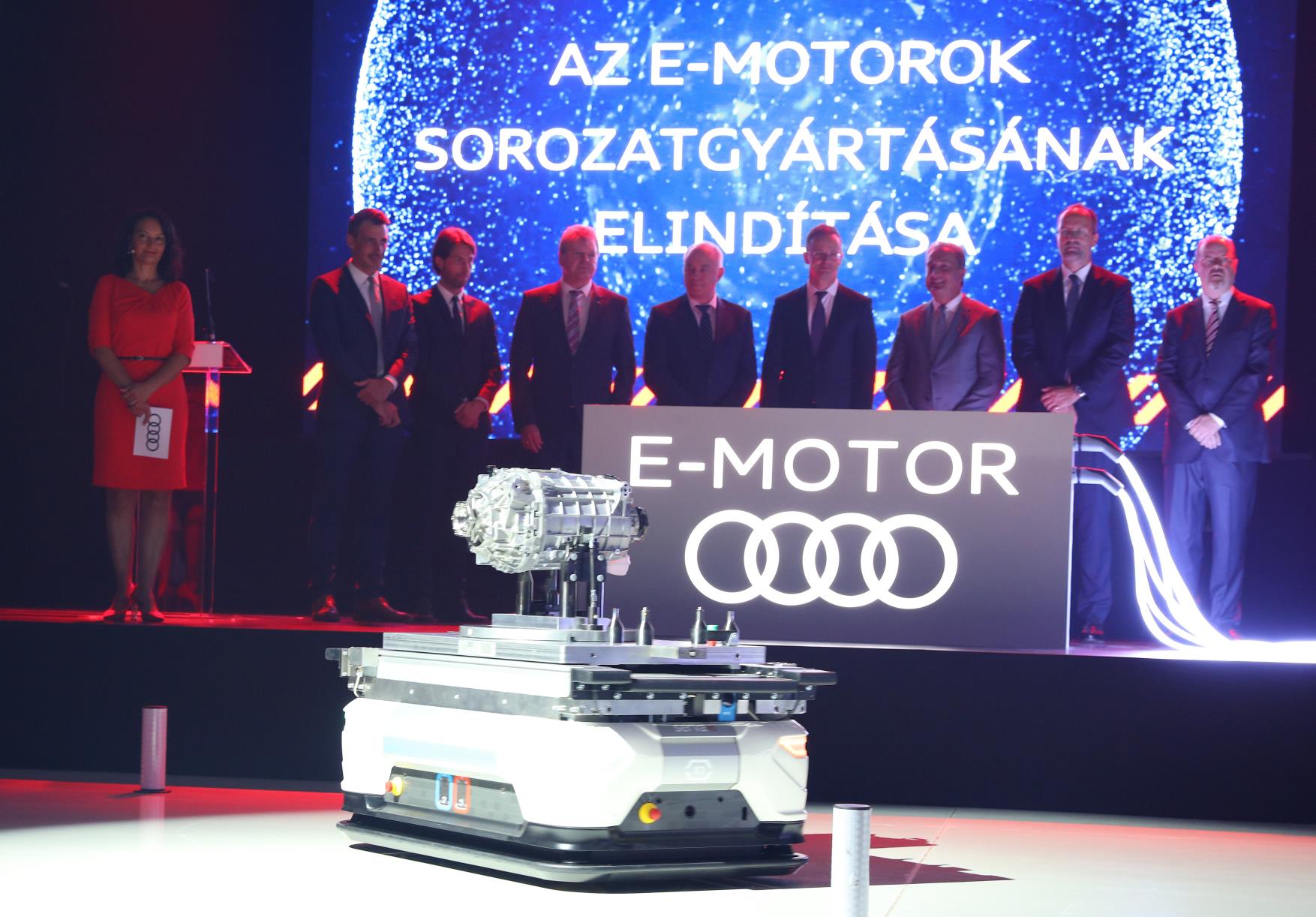
Desde el martes pasado, Audi Hungría comenzó a fabricar en serie sus motores con propulsión eléctrica, que salen desde una fábrica de 8.500 m2, que dispone de un innovador concepto de ensamblaje modular, y que da empleo a un centenar de personas.
Para comenzar este proceso, la filial húngara instaló hace apenas un año los equipos necesarios para la fabricación Los departamentos para el desarrollo de motores eléctricos y para la planificación de la producción trabajaron conjuntamente con el centro tecnológico de producción y fabricación de prototipos en Györ, de cara a adquirir la experiencia necesaria. La capacidad de producción actual es de aproximadamente 400 motores eléctricos al día, y puede incrementarse de forma gradual. Cerca de 100 empleados trabajan en esta nueva área, y la cifra alcanzará los 130 para finales de año. La producción se realiza en un turno, pero pronto pasará a ser de tres turnos.
El motor eléctrico fabricado en Györ ofrece numerosas características nuevas. Con el estator –uno de los componentes principales del motor– el objetivo es bobinar en la carcasa la mayor cantidad de hilo de cobre como sea posible, pues cuanto más compacto sea el devanado, más eficiente es la entrega de potencia. Para ello, Audi Hungría cuenta con un nuevo centro encargado del bobinado y de su inserción en la carcasa. El eje está compuesto de dos elementos de gran tamaño, con la electrónica de potencia integrada en su propio alojamiento, el engranaje y dos palieres que transmiten la potencia a las ruedas. Se fabrican dos sistemas de propulsión, uno por eje, para cada Audi e-tron, modelo que equipa la tracción quattro.
El equipamiento para la producción, los robots y las estaciones de medición y atornillado se establecen en posiciones fijas, pero no están unidas linealmente. En su lugar, los empleados fabrican cada unidad de propulsión en islas de producción independientes, siguiendo un proceso modular. A pesar de contar con una secuencia de ensamblaje predefinida, el sistema modular permite usar rutas ramificadas y liberar espacio en el proceso de producción. Vehículos autónomos, controlados por un sistema IT inteligente, transportan cada módulo a la estación de trabajo correspondiente.
También se instalaron tres bancos de pruebas en el departamentos de desarrollo de motores, para la realización de pruebas y ensayos de carga continua.