Reportajes
Las razones que explican por qué Toyota lo hace bien en medio de la escasez de semiconductores (chips) Parte (I)
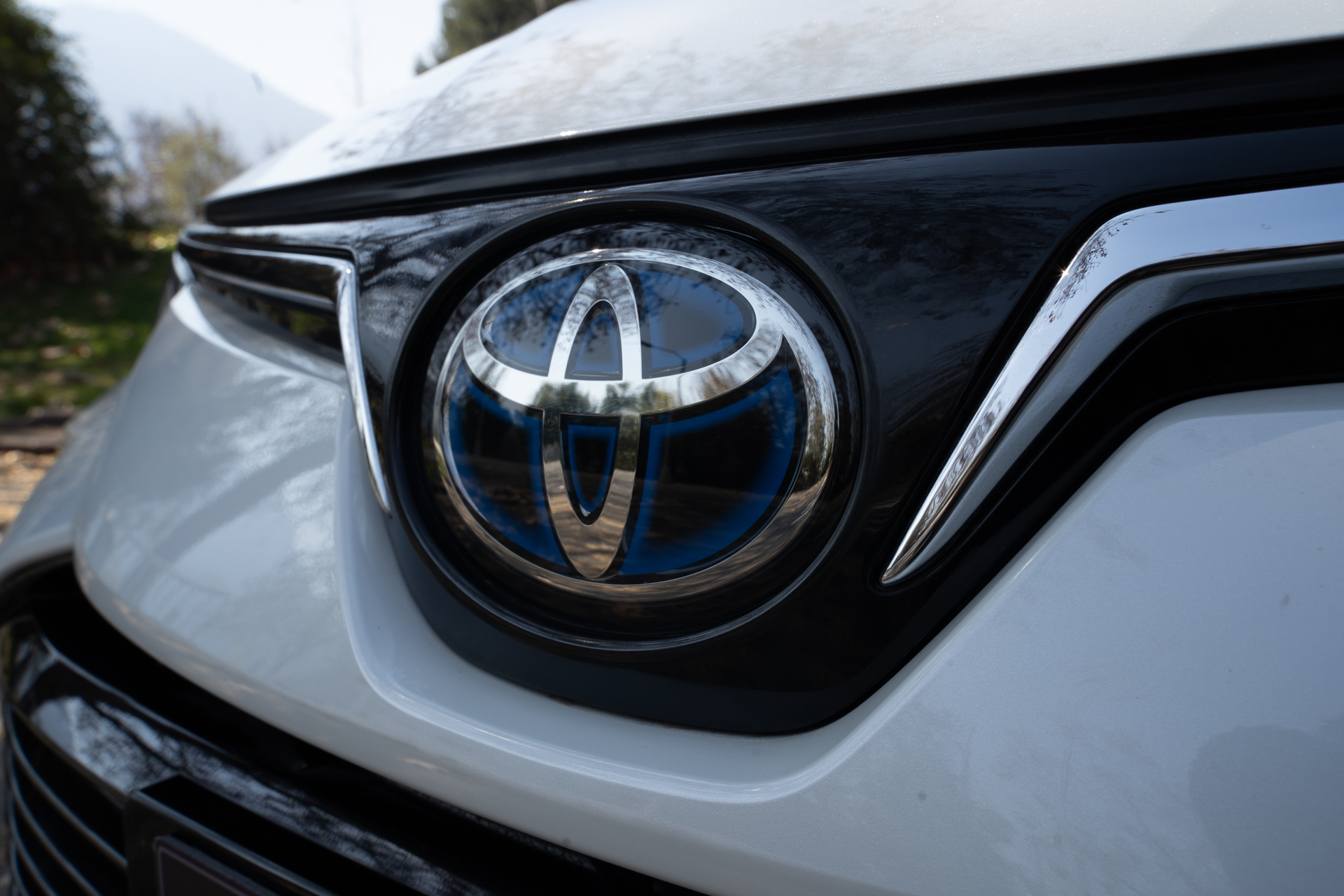
Es posible que Toyota haya sido pionera en la estrategia de fabricación justo a tiempo, pero cuando se trata de chips, su decisión de almacenar lo que se han convertido en componentes clave en los automóviles se remonta a una década antes del desastre de Fukushima.
Después de que la catástrofe rompiera las cadenas de suministro de Toyota el 11 de marzo de 2011, el mayor fabricante de automóviles del mundo se dio cuenta de que el plazo de entrega de los semiconductores era demasiado largo para hacer frente a impactos devastadores como los desastres naturales.
Es por eso que Toyota ideó un plan de continuidad comercial (BCP) que requería que los proveedores almacenaran entre dos y seis meses de chips para el fabricante de automóviles japonés, dependiendo del tiempo que demore desde el pedido hasta la entrega, dijeron cuatro fuentes.
Y es por eso que Toyota hasta ahora ha salido en gran medida ilesa de la escasez global de semiconductores luego de un aumento en la demanda de productos eléctricos bajo bloqueos por coronavirus que ha obligado a muchos fabricantes de automóviles rivales a suspender la producción.
Toyota sorprendió a rivales e inversores el mes pasado cuando dijo que su producción no se vería afectada significativamente por la escasez de chips, incluso cuando Volkswagen, General Motors, Ford, Honda y Stellantis, entre otros, se han visto obligados a reducir o suspender parte de la producción.
Los chips que escasean especialmente ahora son las unidades de microcontroladores (MCU) que controlan una serie de funciones como el frenado, la aceleración, la dirección, el encendido, la combustión, los manómetros de neumáticos y los sensores de lluvia, dijeron las cuatro fuentes a Reuters.
Sin embargo, Toyota cambió la forma en que compra MCU y otros microchips después del terremoto de 2011, que provocó un tsunami que mató a más de 22.000 personas y provocó un colapso mortal en la planta de energía nuclear de Fukushima.
Después del terremoto, Toyota estimó que su adquisición de más de 1.200 piezas y materiales podría verse afectada y elaboró una lista de 500 artículos prioritarios que necesitarían suministro seguro en el futuro, incluidos semiconductores fabricados por el proveedor clave de chips japonés Renesas Electronics. .
Las repercusiones del desastre fueron tan graves que Toyota tardó seis meses en lograr que la producción fuera de Japón volviera a los niveles normales, después de haberlo hecho en casa dos meses antes.
Fue un gran impacto para el sistema justo a tiempo de Toyota porque un flujo fluido de componentes desde los proveedores a las fábricas y las líneas de montaje, así como los inventarios ajustados, fueron fundamentales para su surgimiento como líder de la industria en eficiencia y calidad.
En un momento en el que el riesgo de la cadena de suministro está ahora al frente y al centro en casi todas las industrias, la medida muestra cómo Toyota estaba lista para lanzar su propio libro de reglas cuando se trataba de semiconductores, y está cosechando los frutos.